Mayo Clinic 3D printing its own parts for face shields, N95 masks
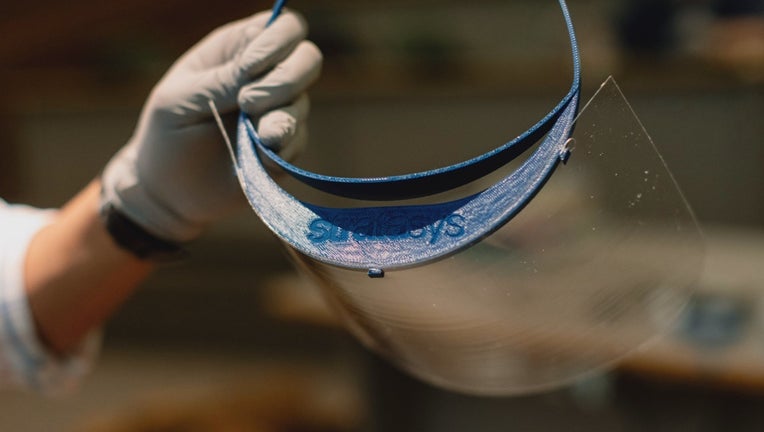
The Mayo Clinic is 3D printing parts to face shields and N95 masks. (Mayo Clinic)
ROCHESTER, Minn. (FOX 9) - The personal protective gear shortage is something Mayo Clinic in Rochester, Minnesota has positioned itself to manage.
Part of its strategy is to manufacture their own components from their 3D printing lab. They’re already printing parts for face shields that Mayo workers are assembling. Dr. Jonathan Morris says they’re working on respirator parts, too.
“We have been working on 3D-printed attachments, so if you look at a respirator, something that 3M makes or other companies make, the mask is already made...if you can imagine a painter with a canister on either side,” said Dr. Morris. “All you need to do is 3D print the attachment and the filter holder... that’s a solution, and our engineering department is working on that solution.”
3D printing not only allows Mayo to make models of the virus itself, it allows them to replace critical tools needed to gather samples and test for the virus.
“We’re testing our ability right now to test nasal swabs,” said Dr. Morris. “Mayo Clinic has the largest ability to do testing of coronavirus to date at an institution. So you can imagine the stress that puts on the number of swabs that you have to put in the nasal cavity to take out. If that supply chain goes down, we’re exploring the ways that we can make 12,000 a day, 94,000 a week, up to a 100,000 a week using additive manufacturing 3D printing at Mayo Clinic.”
With personal protective equipment, Mayo has managed to stretch its supplies by canceling all elective surgeries and procedures. Every employee in a critical setting is now required to wear a face mask, and they’re already prepared to make more if needed.
“That’s the part of us being proactive and pre-emptive to saying this supply chain could be vulnerable,” said Dr. Morris. “It may not be now, but if Minnesota peaks in late April or May it might become crucial for us to be able to manufacture these ourselves. How many can we make out of what material and who can we partner with, and that’s part of engineering’s role in doing that. So we are ramping up production of some things in the tens of thousands locally, but we’re also partnering.”
Mayo has been manufacturing its own components with 3D printing for 14 years. It contributes patterns and research to a special 3D printing exchange at the National Institute of Health that is shared with hospitals all over the country.